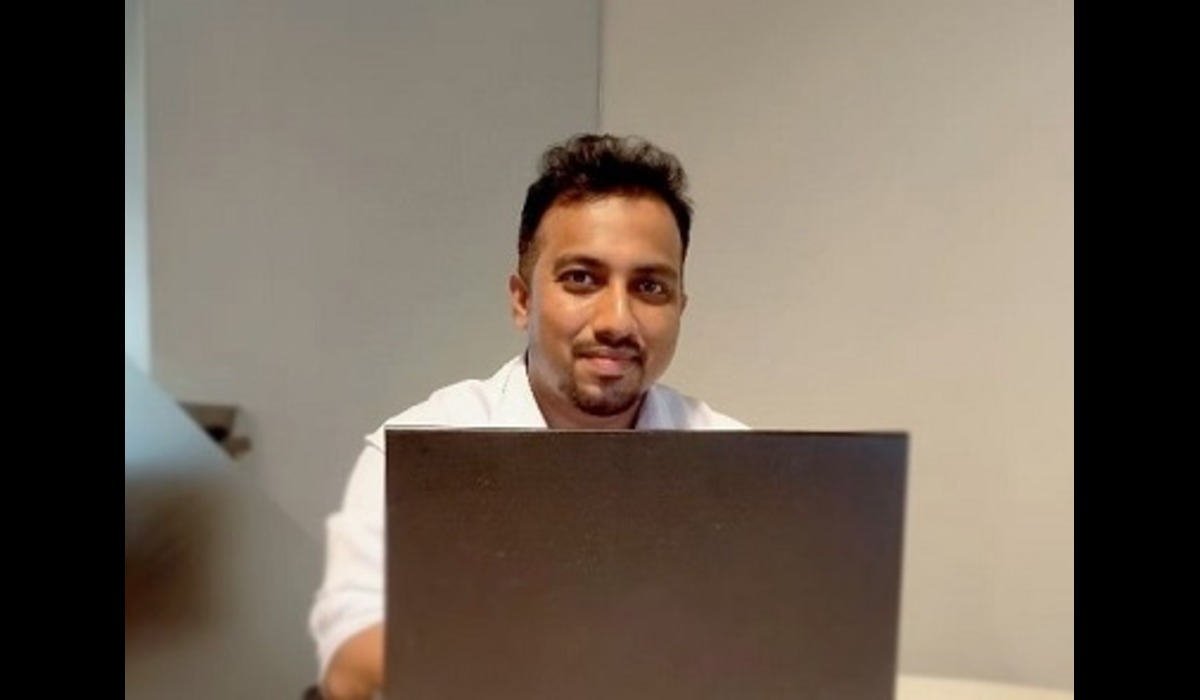
The Responsibility of Cement The Responsibility of Cement The Responsibility of Cement The Responsibility of Cement The Responsibility of Cement The Responsibility of Cement The Responsibility of Cement The Responsibility of Cement The Responsibility of Cement The Responsibility of Cement
Bangladesh’s Progress in 50 Years of Independence
Bangladesh has made significant progress in the 50 years since its independence. While corruption and political instability have hindered the realization of the golden Bengal envisioned, the nation has achieved substantial prosperity in many aspects. The driving force behind this progress is the indomitable and relentless spirit of the people of Bangladesh.
Structural Construction as a Key to Sustainable Development
One of the essential prerequisites for sustainable development is structural construction. Bangladesh is advancing rapidly in this sector. However, the problem is that many of these constructions are not sustainable.
The two primary components of durable construction are steel rebars and cement. Bangladesh has become self-sufficient in producing both of these materials. The country has around 25 steel rebar manufacturing companies and 37 cement manufacturing companies. These companies have the capacity to produce approximately 8 million tons of steel rebars and around 70 million bags of cement annually. Although some claim a higher production capacity, it is practically unattainable. Currently, the demand for steel rebars is about 5.5 to 6 million tons per year, while the demand for cement is around 35 million tons. This indicates that supply is abundant compared to demand.
Approximately 70% of the steel rebar market is controlled by six major companies: BSRM, AKS, KSRM, GPH, Rahim Steel, and Anwar Ispat. These companies maintain high-quality standards in their rebar production. Design engineers specify a particular yield strength for construction, and these companies strictly adhere to those standards. Other companies are gradually improving their quality, ensuring that Bangladesh is relatively secure regarding steel rebars in sustainable development.
Concerns About Concrete Quality
The concern lies with the concrete that encases and supports the steel rebars in infrastructure. The quality of concrete in Bangladesh is quite poor. In most general construction projects, including private houses, mosques, schools, and roads, the standard of concrete is subpar. Even in government, semi-government, and institutional construction projects, the scenario remains the same due to contractor negligence and corruption.
Even if all factors are maintained correctly, the maximum achievable strength is between 2,200 to 2,900 PSI, whereas most engineers design with a concrete strength of 3,000 PSI in mind. To achieve this, a concrete mix ratio of 1:1.5:3 must be maintained, along with several other precautions, such as using high-quality cement, replacing brick chips with stone aggregates, maintaining a minimum FM of 2.5 in sand, using clean water, ensuring the correct water-cement ratio, pouring within the specified time, proper curing, and, in some cases, using construction chemicals. By following these measures, the target strength of 3,000 PSI can be achieved.
The Need for Stringent Concrete Quality Control
Due to the widespread use of high-strength steel Rebar, stricter regulations on concrete strength are now more crucial than ever. Using 72,500 PSI steel rebars with only 2,000 PSI concrete—or sometimes even lower—is akin to aging bones losing their muscle support. As buildings age, they weaken similarly. To match these high-strength steel rebars, a minimum of 3,000 PSI concrete should be used. Renowned concrete specialists and engineers suggest that a combination of 3,500–4,000 PSI concrete is ideal for 72,500 PSI rebars, while at least 3,000–3,500 PSI concrete is necessary for 60,000 PSI rebars. Thus, maintaining a concrete strength of at least 3,000 PSI is now as essential as a fundamental obligation, leaving no room for compromise.
“The Responsibility of Cement Companies in Sustainable Development“
Engr. Md. Golam Hossain Farhan
Issues in Concrete Mixing and Construction Practices
The unfortunate reality is that, in most cases, these additional precautions are not followed. Often, concrete is mixed at a 1:2:4 ratio, and sometimes even this is not maintained. Some private homeowners either fail to maintain the correct mix ratio or neglect other essential precautions. The overall state of concrete quality in the country is chaotic and fragile. As a result, infrastructure is at high risk of earthquake damage and becoming short-lived and prone to collapse under normal conditions.
An interesting phenomenon is that whenever concrete-related issues arise—such as delayed setting, insufficient strength, excessive shrinkage, or structural failure—people immediately blame the cement companies.
The Role of Cement Companies in Ensuring Concrete Quality
Out of the 37 cement manufacturers in the country, most advertise their cement strength based on lab-tested cube results, which show values of 4,000 PSI, 5,000 PSI, or even 6,000–7,000 PSI. This creates confusion among consumers, leading masons to learn incorrect practices and some engineers to make errors in concrete mix design. Consequently, we end up with fragile and short-lived concrete structures.
In recent years, several companies have been offering ready-mix concrete services. However, the adoption rate has not been as expected. These companies have struggled to gain the trust of private construction owners and establish business relationships with contractors. With a few exceptions, many ready-mix companies fail to maintain consistent quality. The ones that do maintain their promises have found success in national mega projects and infrastructure development. Unfortunately, deceptive practices, such as misleading information about cement properties, are becoming increasingly common.
Major Cement Companies Must Take Responsibility
Among the cement manufacturers, 14 companies with at least a 2% market share each control around 85% of the market. These include Shah, Fresh, Bashundhara, Holcim, Crown, Seven Rings, Scan, Premier, Akij, Aman, Confidence, Tiger, Bengal, and Anwar. These companies bear significant responsibility for ensuring sustainable construction.
To fulfill this responsibility, cement companies should adjust their promotional strategies. In addition to highlighting the quality of their cement, they should emphasize best practices for producing high-quality concrete.
Steps Cement Companies Can Take:
- Training and Awareness Programs: Cement companies should conduct field-level seminars and training workshops to educate homeowners, engineers, and masons about proper concrete mixing and construction techniques.
- Educational Promotional Materials: Companies should include short messages about concrete quality in their promotional items, such as calendars, leaflets, brochures, and profiles.
- Media Awareness Campaigns: TV advertisements, newspaper ads, and billboards should incorporate messages about quality concrete production.
- Industry Leadership: Large cement companies should lead by example. If they change their messaging, smaller companies will follow suit.
Conclusion
Our expectation is that cement companies will take a leading role in ensuring high-quality concrete for the nation’s sustainable construction. By doing so, they will not only serve their own interests but also contribute to the country’s long-term development.
This article was originally published on June 12, 2021, on Bangla Daily 24 under the title “The Responsibility of Cement Companies in Sustainable Development.”