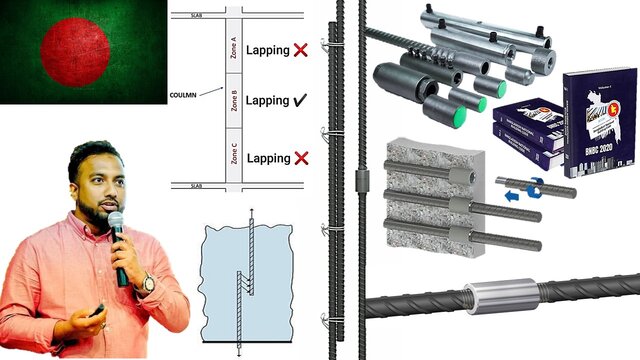
With Rebar Coupler Connections Build a Stronger Bangladesh
“After 52 years, 7 months, and 20 days of independence, a country has become independent once again. Its name is Bangladesh Version 2.”
It is now ranked as the 35th economically strongest country in the world and the 13th in Asia. This newly re-independent nation has made remarkable progress over the past decade, despite rampant corruption and economic mismanagement.The clearest indicator of this development has been the country’s structural growth, which can be measured by the increasing demand for steel and rebar.
In the last fiscal year, Bangladesh’s total demand for steel was approximately 6,112,009 metric tons, which was around 5,945,370 metric tons just two years earlier, during the 2021-22 fiscal year.
With this growing demand for steel and construction materials,
comes the increased consumption of fuel needed for production, a rise in carbon emissions, higher spending of foreign currency on raw material imports year after year, as well as the escalating use of groundwater and natural gas.
“Modern construction no longer destroys civilization; it advocates for the green revolution.”
In modern construction, high-strength rebars are now being used, which are much stronger, more economical, earthquake-resistant, and eco-friendly compared to traditional rebars.
Most importantly, the use of these high-strength rebars can reduce the overall demand for steel in the country,
ultimately saving energy, and foreign currency, and reducing carbon emissions. It’s not just high-strength rebars; changes are also being made in construction techniques to reduce the use and cost of rebars. One such technique is the use of “couplers” or mechanical joints for rebars.
What is a coupler or mechanical joint for rebars?
It is a modern method of connecting rebar to rebar in construction.
A coupler, also known as a mechanical joint, is a device that mechanically connects the ends of two rebars. Typically made of metal, the coupler creates a strong bond by threading and tightening around the ends of the rebars. Using a coupler provides a strong, balanced, and permanent connection between the rebars, which is far more reliable and effective than traditional lapping. The advantage of using couplers is that they allow for quick and easy connections, reducing both construction time and costs.
What is lapping?
Lapping is a process where the ends of two rebars are overlapped and pressed together. In this method, the ends of the rebars merge to form an integrated section.It is commonly used with steel rebars and involves the use of copper wire or welding for structural connections. The connection created through lapping is typically reinforced with cement concrete or other materials to ensure strength. Although the lapping process is relatively simple, it can be time-consuming and labor-intensive, often requiring additional force or materials to ensure reliability.
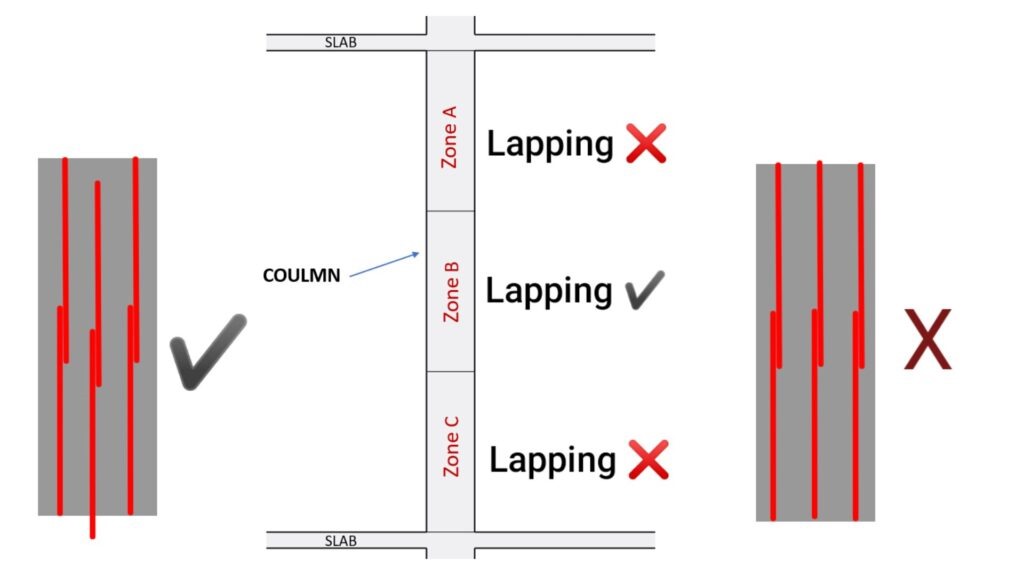
Why is a coupler better than lapping?
The use of couplers or mechanical joints in construction not only simplifies the process compared to lapping but also makes the joint significantly stronger, saving both time and costs in construction. This method is supported by international construction codes, particularly for earthquake-resistant structures, where it is considered essential.
If we first talk about ease of construction, connecting rebars through couplers or mechanical joints is an extremely simple task.
Currently, two of Bangladesh’s largest steel manufacturers import couplers from two renowned international companies, Dextra and Leviat, sourcing them from Thailand and Malaysia, respectively, to supply to their users. During delivery, these companies cut the rebars to the required length and thread their ends according to standards.
At the construction site, one simply needs to insert half of the designated coupler into the threaded end of the first rebar by rotating it, and similarly connecting the other rebar to complete the joint. It’s a very straightforward and efficient process.
Recently, a professor from Bangladesh University of Engineering and Technology (BUET), has been working on developing a method for producing couplers in Bangladesh and threading the rebars on-site by skilled technicians. We hope that we will soon receive modern and high-quality construction materials from this esteemed academic institution, which will further simplify our construction techniques.
Secondly, let’s talk about the time-saving benefits of construction.
Since the two steel manufacturing companies cut the rebars to the required size and thread the ends according to standards at their factories, they also neatly package the couplers along with the rebars.
As a result, any worker at the construction site can quickly and accurately install the rebars, following the drawing or plan, without much effort or time. This eliminates the hassle of cutting rebars, tying them with copper wire, or welding on-site, which saves a significant amount of time during the construction process.
Thirdly, mechanical joints or coupler joints are stronger and safer than lapping because the strength of lapping depends on several factors, such as:
1. Whether the correct lapping length is being followed according to the code for each rebar diameter and grade, which is often not adhered to or even known in many cases in our country.
2. The proper binding or welding with copper wire or binding wire.
3. The strength of the concrete, which is a crucial factor.
In other words, the strength of lapping is not independent but dependent on many other factors.
On the other hand, a coupler or mechanical joint is an independent and much stronger method for connecting two rebars. You might be surprised to know that a high-quality mechanical joint or coupler joint is often stronger than the rebar itself. This is because one of the key conditions of a coupler joint is that in a load test, the rebar will break, but the joint will remain intact, and the break will occur away from the joint. It is completely independent and does not rely on the strength of the concrete or any other factors. Thus, it ensures a secure and reliable load-bearing connection from the foundation to the peak.
Fourthly – Earthquake Resistant:
To construct earthquake-resistant buildings or structures, it is crucial to arrange the rebars correctly at the beam-column joints and ensure proper placement of all rebars in the foundation.
Another important aspect is that the connection of rebars through lapping or welding must occur at specific locations of the beams and columns, where the moment is zero.
However, such connections should never be made inside or near the beam-column joints. In practice, many workers, to minimize waste, connect the rebars close to or within the beam-column joints, putting the building at risk of collapse during an earthquake. Using rebar couplers increases the flexibility in the placement of rebar connections, making the building not only earthquake-resistant but also reducing waste.
During an earthquake, the outer rebars can sometimes develop cracks and fail, which prevents the lapped rebars from bearing any load. In contrast, rebars connected using couplers can easily take the load. Therefore, rebar couplers are essential for constructing earthquake-resistant buildings.
Fifthly – Avoiding Rebar Congestion:
The use of high-strength rebars helps reduce congestion at beam-column joints, and the application of couplers maintains this benefit when connections between rebars are necessary at those joints. This not only allows the concrete to flow easily but also strengthens the joints, making them more durable and suitable for all types of disasters, including earthquakes.
Now, let’s discuss the most important aspect of our country: The cost comparison
For rebars with a diameter of 20 millimeters or more, coupler joints are undoubtedly more economical compared to lapping. In some cases, a similar or slightly lesser expense is seen for 16-millimeter rebars.
Considering safety and costs, building codes in various countries have encouraged the use of couplers instead of lapping for larger-diameter rebars.
However, it is essential to compare the total lapping costs of a project with the total costs of using couplers. Often, engineers in our country make the mistake of comparing a coupler joint with a lapping joint. As I mentioned before, the biggest disadvantages of lapping are twofold.
Firstly, in most cases, the lapping length is not calculated correctly, and an arbitrary factor of 50 is assumed. Secondly, lapping cannot be applied everywhere; it can only be done in lapping zones, that is, in areas of the construction frame where the moment is zero. However, in many cases, rebar workers or contractors apply lapping wherever the rebar ends, which is against the code and extremely risky for construction.
Therefore, according to the code (BNBC Code 8.2.3.3), the lapping length must be kept accurate, and the costs for rebars should be calculated accordingly. To maintain proper lapping zones, there is significant rebar wastage in the project, which should be included in the lapping costs, along with cutting costs, copper wire or welding costs, and labor costs. It is noteworthy that the total number of lap joints in a project is at least 25% more than the total number of couplers or mechanical joints,which is undoubtedly another important aspect of cost comparison.
What types of couplers and threading are available?
Based on construction needs, various types of couplers are available in Bangladesh. These include:
1. Regular Threaded Coupler (commonly known as just “coupler”)
2. Reducer Threaded Coupler (similar to the regular threaded coupler but can connect rebar of larger and smaller diameters)
3. Headed Coupler, Terminator Coupler, or Anchor Coupler (regardless of the name, this type serves to hold the ends of rebar in place)
4. Additionally, Punching Couplers and MBT Couplers are used in situations where threading the rebar is not feasible.
Regarding the types of threading, there are primarily two types: Type One and Type Two.
Type One Thread is created by shaving the surface of the rebar, which I do not prefer, nor does the code.
This type of threading can be used for general purposes.
Type Two Thread is created by forging, maintaining the quality of both the connection and the rebar
Threading can also be classified into three types based on functionality:
Type-A Half Thread (where half the length of the coupler is threaded,
allowing the coupler to connect a half of one rebar and a half of another)
Type-B Full Thread (where the length of the coupler is fully threaded,
allowing the entire coupler to be inserted into one rebar for construction purposes)
Type-C Extended Thread (where a full coupler length is threaded along with some additional length to accommodate a thick lock nut called a lock nut,
making the mechanical joint the strongest).
However, based on cost and functionality, the demand for Half Thread or Type-A is higher for most construction projects in our country.
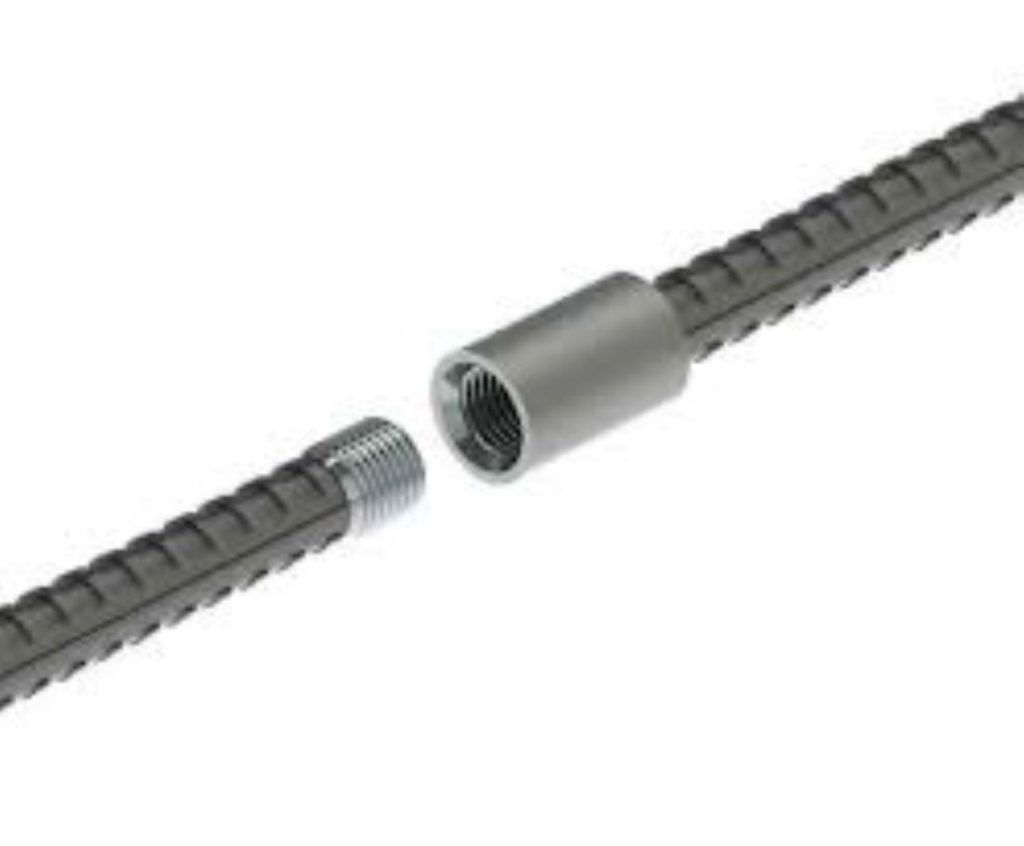
Where can you find the best coupler services in Bangladesh?
In our country, apart from the couplers from two major steel manufacturing companies, Dextra and Levitate, there are several smaller companies providing coupler services.
However, in most cases, these smaller companies often deal with low-quality couplers imported from China and India.
It is worth mentioning that, as of now, no one in our country officially manufactures couplers, unless someone in Jinjira is creating counterfeit couplers.
The most critical aspect of couplers is the threading,
which is not done to standard by anyone except for the two large companies. A notable concern in threading is whether the diameter of the rebar or the surface gets damaged. Most ordinary companies employ a method of threading under the guise of site support, which severely damages the surface of the rebar and significantly reduces its strength at that specific point.
We know that currently, most rebar is produced using the Thermo Mechanical Treatment (TMT) method, allowing the surface of the rebar to withstand the highest load.
Therefore, if someone shaves off the surface of the rebar and then covers it with a low-quality coupler, the likelihood of the rebar connection breaking during an earthquake increases significantly.
The two large steel manufacturing companies import couplers from Malaysia and Thailand, and they also employ experienced mechanical engineers who forge the ends of the rebar and then roll thread them, ensuring that the surface remains intact and strong, which guarantees earthquake resistance.
When ordering rebar from these companies, they will cut, thread, and pack the rebar according to your design along with the couplers, making it easy for you to install them on-site without any hassle.
It is noteworthy that a respected professor at Bangladesh University of Engineering and Technology (BUET)
is currently working on modern and qualitative methods for producing couplers and providing threading services on construction sites.If he can provide a product that meets the standards and is comparable to or even better than those from the two large steel manufacturers,it would certainly be a great fortune for us, making our construction safer and more cost-effective.
How to Understand the Best Coupler?
To determine whether a coupler is good or bad, it is essential to understand the entire mechanical joint.
This means that the coupler supplier must ensure the quality of both the coupler and the threading in such a way that when a paired rebar is subjected to tension in a laboratory setting, it does not exceed the maximum load-bearing capacity or tensile strength of that rebar.
In other words, the rebar should break or fail at the tensile strength level, but the coupler itself should not fail, loosen, or come apart.
Additionally, there should be no tearing at the threaded part of the rebar or in its vicinity; the rebar should fail away from the threading area.If this is not the case, it indicates that there may be issues with the mechanical joint.
In Conclusion, the Code Matters
The most modern method of connecting rebars should be included in the code. The Bangladesh National Building Code (BNBC) 2020 mentions mechanical joint couplers.
As for ACI, which is followed and referenced by the BNBC, it has long addressed this issue.If you look into ACI 318-19 regarding mechanical joints, you will find a lot of guidance, InshaAllah.Building Code 8.2.12.3 (d), it encourages the avoidance of using Type One threaded couplers in special moment frames.Meanwhile, section 8.3.5.3 states that lapping should not be done haphazardly and can only be performed in the middle of a member where the moment is zero.At the same time, sections 8.2.12.3 (a) to 8.2.12.3 (d) allow the use of mechanical joints or couplers anywhere in the member.
This has been detailed multiple times in my previous discussions.
So, engineers and contractors, let’s end the era of lapping in construction work and join rebars with couplers to build a modern, easy, durable, robust, and cost-effective Bangladesh.
This article was published in Kalerkontho online portal on 7th October 2024 https://www.kalerkantho.com/online/miscellaneous/2024/10/07/1432818